An operations manager at a funfair company has been jailed for six months and disqualified as a director for five years after a three-year-old girl died on a Norfolk beach. The funfair company he was working for has been fined £20,000.
The inflatable trampoline Ava-May Littleboy had been playing on exploded, ejecting her high into the air.
Ava-May, from Somersham in Suffolk, had been taken by family and friends to the Bounce About attraction that had been set up on the beach at Gorleston-on-Sea in Norfolk, on July 1, 2018.
She and a nine-year-old girl were on the trampoline when the blast happened without warning. While the older child suffered minor injuries, Ava-May was thrown upwards – witnesses described her as being shot up between 20 and 40 feet, or the height of a house. She landed on the beach. In the process, she sustained fatal head injuries.
In a tribute, Ava-May’s mother said a family tradition is now to spend Ava-May’s birthday at her bench in the local park.
Johnsons Funfair Limited, trading as Bounce About, operated a number of bouncy castles, slides and other inflatables on the beach at Gorleston, and at another site on Great Yarmouth beach.
Great Yarmouth Borough Council worked with the Health and Safety Executive (HSE) on a joint prosecution. Charges were brought against Johnsons Funfair Limited and its operations manager, Curt Johnson, whose wife was sole owner and director of the company.
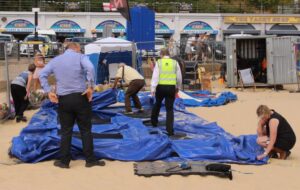
The investigation found that Curt Johnson, on behalf of the company, had imported the inflatable trampoline into the UK from China in 2017 and had put it into use without carrying out any of the required testing and certification to ensure it was safe to be used by the public. An importer of such an item equipment must ensure that there has been a proper review of the design, verification that the item has been manufactured in accordance with the design, and a detailed test by a suitable expert on the item’s arrival in the UK. None of that had been done here.
In operational terms, there had been no proper risk assessment or work procedure laid down, and the company used undertrained staff paid cash in hand, some of them too young to work without child work permits which were not sought and would not have been granted for work at such a fairground.
Crucially, the defendants allowed the company’s inflatables (which included a number of other inflatables besides the trampoline which exploded) to be operated despite not having, and not seeking, any operating instructions from the manufacturer, and without having their inflatables properly annually checked and certified by an independent expert under the ADIPS scheme (a scheme for checks comparable to MoT checks for vehicles).
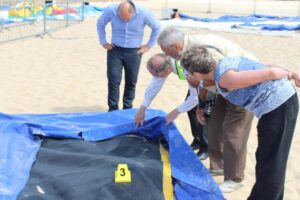
HSE’s long-established guidance can be found at: Health and safety guidance for fairgrounds (hse.gov.uk). Guidance more specific to sealed inflatables can be found at: Sealed inflatables: safe supply, inspection and operation – Overview – HSE.
Chloe Littleboy, Ava-May’s mother, said: “Birthdays are always at her bench in the park. Balloons, flowers, cakes and sweets decorate it and the whole family go there together to celebrate. That’s now the family ‘thing’, spending her birthday, Christmas and the anniversary of her death all together.”
Nathan Rowe, Ava-May’s father, added: “It’s amazing as a parent that so many people care about your child. It’s surprising how one little girl had impacted on so many lives. I read her eulogy and it was my one and only chance to pay tribute to her and her short life. I don’t know of another father who’s had to do this.”
Johnsons Funfair Limited, of Swanston’s Road, Great Yarmouth, as importer and site operator, pleaded guilty to breaching Sections 6(1A)(a) and 3(1) of the Health and Safety at Work etc. Act 1974. The company was fined £20,000 and ordered to pay £288,475.62 in costs.
Curt Johnson, of Swanston’s Road, Great Yarmouth, pleaded guilty to offences of having consented to or connived in each of the company’s two offences, or those being attributable to his neglect. Johnson was sentenced to six months in custody for each offence, to be served concurrently, and disqualified as a director for five years.
The sentences were passed at Chelmsford Magistrates’ Court.
HSE principal inspector Ivan Brooke said: “Our thoughts today are with the family of Ava-May. This was supposed to be a fun day out, but it ended in tragedy.”
“The operator flouted the rules on certification and testing to devastating consequences.”
“Had the company carried out the required checks, and followed the freely available, well-established guidance, this tragedy would not have happened.”
“Since the tragedy, and following the inquest, we published supplementary guidance more specific to sealed inflatables. They should be checked over by the responsible body before they are used, and maintained effectively throughout.”
“Incidents with inflatables are extremely rare, but we will not hesitate to take strong action if funfairs do not take the required precautions.”
James Wilson, head of environment and sustainability at Great Yarmouth Borough Council, said: ‘’It has been five years since Ava May died so tragically during what should have been a safe family day out at the beach.”
“The safety of the public is of paramount importance and it was essential Great Yarmouth Borough Council and our partners at the Health and Safety Executive carried out a thorough investigation to try to ensure such a tragedy is not repeated.”
“The prosecution and sentencing of those responsible finally brings some closure to what has been an unbearably difficult time for Ava May’s family and the council is pleased justice has been served.”
“We hope this case highlights how operators must ensure safety of their customers at all times.’’
The prosecution was supported by HSE enforcement lawyer Kate Harney and by Norfolk County Council solicitor David Lowens.
Notes to Editors:
- The Health and Safety Executive (HSE) is Britain’s national regulator for workplace health and safety. We prevent work-related death, injury and ill health through regulatory actions that range from influencing behaviours across whole industry sectors through to targeted interventions on individual businesses. These activities are supported by globally recognised scientific expertise. hse.gov.uk
- The Great Yarmouth Borough Council (GYBC) is the local authority for the Great Yarmouth area, including Gorleston, and it has health and safety enforcement responsibility for certain premises in its area, including the site run by Johnsons Funfair Limited.
- More about the legislation referred to in this case can be found at: legislation.gov.uk/
- HSE news releases are available at http://press.hse.gov.uk
- HSE guidance on fairgrounds and amusement parks can be found here – Fairgrounds and amusement parks: Guidance on safe practice – HSG175 (hse.gov.uk)
- HSE guidance on sealed inflatables can be found here – Sealed inflatables: safe supply, inspection and operation – Overview – HSE.
- Curt Johnson, of Swanston’s Road, Great Yarmouth, pleaded guilty to breaching Section 6(1A)(a) and Section 3(1), by virtue of Section (37)(1), of the Health and Safety at Work etc. Act 1974.