HSE launches manufacturing inspection initiative focusing on respiratory risks from silica
Health and Safety Executive (HSE) inspectors have begun a targeted inspection initiative focusing on manufacturing businesses where materials that contain silica are used. This will include brick and tile manufacturers and foundries.
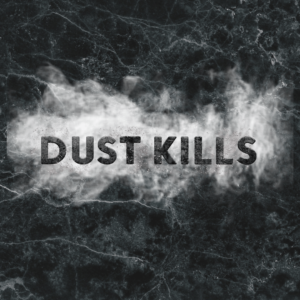
Exposure to airborne particles of respirable crystalline silica (RCS) can lead to life-changing respiratory conditions such as silicosis, chronic obstructive pulmonary disease and lung cancer.
Silica is a natural substance found in most stones, rocks, sand, and clay. Silica particles are produced during many manufacturing tasks involving these materials. Over time, exposure to silica particles can harm a worker’s ability to breathe and cause irreversible, often fatal, lung diseases.
The inspections, which start today (Monday 3 July), are checking that employers and workers know the risks involved when dealing with RCS and that businesses have control measures in place to protect workers’ respiratory health.
The initiative is supported by HSE’s Dust Kills silica campaign. This provides straight forward advice and guidance on the Work Right website for employers and workers, to help everyone understand the risks and how to protect respiratory health when processing materials that contain silica: https://workright.campaign.gov.uk/campaigns/silica/
Employers have a legal duty to create suitable arrangements to manage health and safety and ensure they comply with the Control of Substances Hazardous to Health Regulations 2002 (COSHH). Inspectors will be looking for evidence that businesses have put in place effective control measures, such as Local Exhaust Ventilation (LEV), and where appropriate, use of water suppression and personal protective equipment such as Respiratory Protective Equipment (RPE), to reduce workers’ exposure to the RCS. If any health and safety breaches are discovered, HSE will take enforcement action to make sure workers’ health is protected.
HSE’s head of manufacturing David Butter said: “It’s important that manufacturing businesses act now to ensure they comply with the law and protect their workers from serious lung diseases. Businesses should take note that good ventilation in the workplace and personal protective equipment are just some of the measures they need in place to protect the respiratory health of workers.
“During the 2022 silica initiative, inspection findings indicated poor management of control measures including engineering controls, cleaning and housekeeping and RPE management. Employers should ensure control measures are used and maintained appropriately.
“We want employers and workers to make sure they are aware of the risks associated with the activities they do. For example, brick and tile manufacture and foundry activities can create RCS dust that could be breathed in. To assist them we have advice and free resources on our Dust Kills campaign pages.”
To view the guidance visit:
- https://workright.campaign.gov.uk/campaigns/silica/silica-employers/brickandtile/
- https://workright.campaign.gov.uk/campaigns/silica/silica-employers/foundries/
- Or download our advice for workers: https://workright.campaign.gov.uk/download/6194/?tmstv=1688117586
You can sign up for regular updates on the silica campaign here. Follow the campaign on Twitter at @H_S_E or on Facebook @hsegovuk.
Notes to editors:
- The Health and Safety Executive (HSE) is Britain’s national regulator for workplace health and safety. We prevent work-related death, injury and ill health through regulatory actions that range from influencing behaviours across whole industry sectors through to targeted interventions on individual businesses. These activities are supported by globally recognised scientific expertise.
- Further details on the latest HSE news releases is available.
- The inspection programme will be supported by HSE’s ‘Dust Kills’ campaign, aimed to influence employer behaviour change.