Tata Chemicals fined following young father’s death
Tata Chemicals Europe Limited has been fined after a young father died following an incident while erecting a scaffold tower in a chemical plant in Northwich.
Michael Densmore, from Halewood in Merseyside, died following complications to the wound he sustained after his right foot slipped into a trough containing a liquid chemical calcium hydroxide – more commonly known as ‘milk of lime’ – causing chemical and thermal burns.
The 37-year-old father-of-four was one of a number of scaffolders employed by Altrad NSG to erect scaffolding at Tata’s Lostock Hall site.
On 30 November 2016, during the course of this work, Mr Densmore stepped over a trough which contained milk of lime – which had been heated to approximately 90 degrees centigrade. His right foot slipped on an unfastened lid covering the trough, resulting in him sustaining chemical and thermal burns to his foot and ankle.
He was airlifted to Whiston Hospital burns unit, where he received specialist treatment and underwent surgery on 8 December and was discharged just over a week later. However, on 3 January 2017, while at home, he suffered a haemorrhage to his right foot and was taken to hospital following a 999 call, but tragically died.
In a statement issued by his family, Micheal was described as ‘a loving and amazing role model’ to his sons and two nieces.
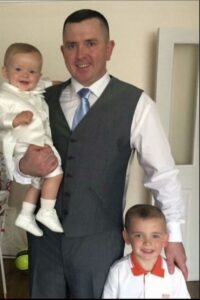
“Our lives fell apart and have not been the same since that terrible day,” they said. “Nobody should have to lose someone they love, due to an accident that happened at work.
“A mother should never have to give CPR to her own son, and a partner, should never have to tell their children that their dad will not be coming home.
“Michael has missed so many life events in the past seven years, including missing his nieces having their own babies, his eldest son giving him a grandson, his youngest boys communions, to name just a few.
“What hurts us the most is the fact that he will never be able to complete all the plans he had for life, including marrying his Helen.
“The trauma, we have all suffered as a family, cannot truly be put into words. We were once a small happy close-knit family, who all lived life to the full, with Michael being the leader and now we just about get through each day.”
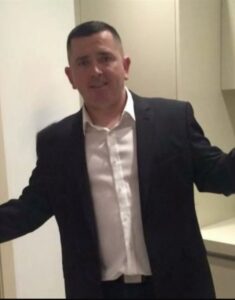
The Health and Safety Executive (HSE) investigation found there was no permit in place for hazardous work in a live chemical plant. Little proper thought had been given to the risks involved by those responsible for ensuring staff safety. As far as the scaffolding team was concerned, there was no clearly understood plan to address these risks. Mr Densmore had only received a brief induction when he started work on the site some months before. Crucially, he had not been warned that there would be chemical product flowing through the plant and that the lids to the trough had not been properly sealed. Tata employees had been seen working on or near the troughs and there were no visible warning signs in place.
It also found that there had been previous prosecutions of Tata Chemicals Europe relating to health & safety failures at Lostock Hall and nearby Winnington Lane.
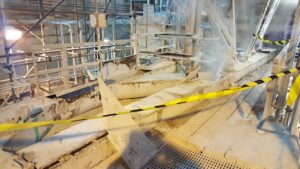
Tata Chemicals Europe Limited, of Winnington Lane, Northwich, Cheshire pleaded guilty to breaching Section 3(1) of the Health and Safety at work etc. Act 1974. The company was fined £1.125 million and ordered to pay £60,603.54 in costs at Chester Crown Court on 5 June 2024.
Speaking after the case, HSE inspector Matt Lea said: “This tragic death could have been preventable had Michael Densmore and his colleagues been managed under a robust permit to work system for working in a live chemical plant containing corrosive chemicals which had been heated almost to boiling point.
“Michael should not have been put in this unsafe working situation and should have been warned about the dangers of stepping over the troughs and that they were still in operation.
“Companies should learn the lessons from this incident if they have staff or contractors working in a similar environment and be aware that HSE will not hesitate to take appropriate enforcement action against those that fall below the required standards.”
This prosecution was brought by HSE enforcement lawyer Chloe Ward and supported by HSE paralegal officer Sarah Thomas.
Notes to Editors:
- The Health and Safety Executive(HSE) is Britain’s national regulator for workplace health and safety. We prevent work-related death, injury and ill health through regulatory actions that range from influencing behaviours across whole industry sectors through to targeted interventions on individual businesses. These activities are supported by globally recognised scientific expertise.
- More information about the legislationreferred to in this case is available.
- Further details on the latest HSE news releasesis available.