Companies fined as child suffers fractured skull
Three companies have been fined a total of £420,000 after a slate tile fractured the skull of a three-year-old child.
The slate came off a roof at a construction site at the Moonfleet Manor hotel in Weymouth, Dorset, and struck the young girl on 13 June 2019.
She had been leaving the hotel with her father and older brother after attending a swimming lesson.
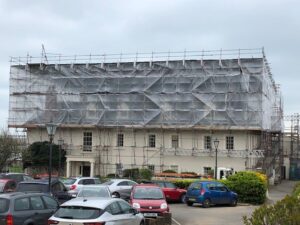
The pre-schooler received first aid and was later taken to hospital where she was put into an induced coma to stabilise her. She then underwent a two-hour operation to remove fragments of slate from her head.
The slate had come off the hotel roof and fell approximately five metres before striking the child.
The roof was being renovated by Rocare Building Services Limited.
The company had taken off the old tiles and began replacing them with new slates.
The new slates had been stacked around the roof, leading to one piece falling off.
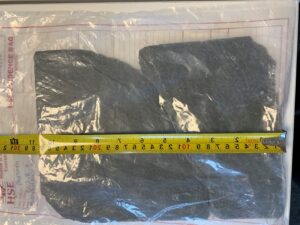
Rocare Building Services Limited had been appointed by Moonfleet Manor as the principal contractor to oversee the refurbishment work which also included replacing windows and restoring chimneys and gutters.
Quadra Built Environmental Consultancy Limited had been hired by Moonfleet Manor as the principal designer, in charge of planning, managing and monitoring the pre-construction phase. The company failed in the planning and design stage to properly assess the risks of objects falling from height and hitting people. There was insufficient consultation and collaboration between the various duty holders.
A Health and Safety Executive (HSE) investigation into this incident found scaffolding was not fit for purpose because it did not have sufficient measures to prevent items falling such as protective fans, covered walkways or, at a minimum, brick guards around the entire perimeter. Such measures are cheap and readily available within the industry. Moonfleet Manor ignored requests and failed to put in measures to address an obvious hazard of falling objects coming into contact with members of the public using the busy thoroughfare to the swimming pool. Moonfleet Manor was more concerned about putting convenience of the guests and preventing the hotel from looking like a building site than the safety of their guests, the judge found.
HSE guidance can be found at: Construction – Planning for construction work (hse.gov.uk)
At Bournemouth Crown Court on 24 October 2023:
- Rocare Building Services Limited, of Headlands Business Park, Salisbury Road, Ringwood, Hampshire, pleaded guilty to breaching Regulation 13(1) of the Construction (Design and Management) Regulations 2015 and Regulation 10 (1) of Work at Height Regulations 2005. The company was fined £160,000 and ordered to pay costs of £15,554.78.
- Quadra Built Environmental Consultancy Limited, of Kingsmead, Lechlade On Thames, Gloucestershire, was found guilty of breaching Regulation 11 of the Construction (Design and Management) Regulations 2015. The company was fined £60,000 and ordered to pay £25,000 in costs.
- LFH (Moonfleet Manor) Limited, of Manfred Road, Putney, London, was found guilty of breaching Section 3(1) of the Health and Safety at Work etc. Act 1974. The company was fined £200,000 and ordered to pay £143,482.04 in costs.
HSE inspector Nicole Buchanan said: “This incident has caused significant injuries and extreme distress to a child and her family; and could have been fatal.
“Clients and construction companies must always remember their legal duty to keep both workers and members of the public safe. The client, principal designer and principal contractor all have a duty to work together to implement the industry standards to ensure members of the public are safe particularly if a venue is to remain live.”
This HSE prosecution was supported by HSE’s appointed legal team Sam Jones and Blake Morgan’s Steve Parish.
Notes to Editors:
- The Health and Safety Executive (HSE) is Britain’s national regulator for workplace health and safety. We prevent work-related death, injury and ill health through regulatory actions that range from influencing behaviours across whole industry sectors through to targeted interventions on individual businesses. These activities are supported by globally recognised scientific expertise. hse.gov.uk
- More about the legislation referred to in this case can be found at: legislation.gov.uk/
- HSE news releases are available at http://press.hse.gov.uk
- A neurologist who assessed the child is hopeful they will make a full recovery, the court heard.